Sommerset’s Asphalt Paving Services
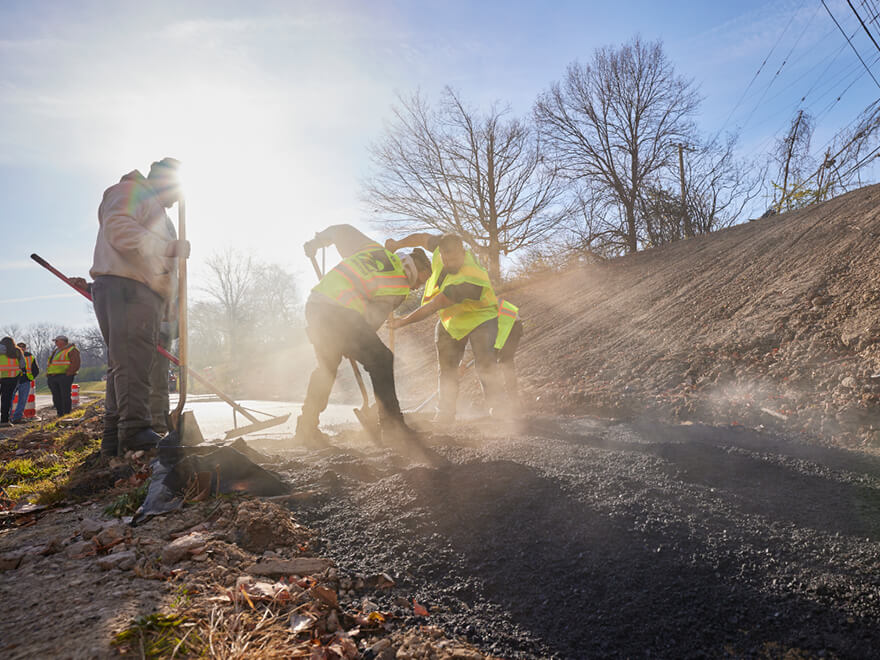
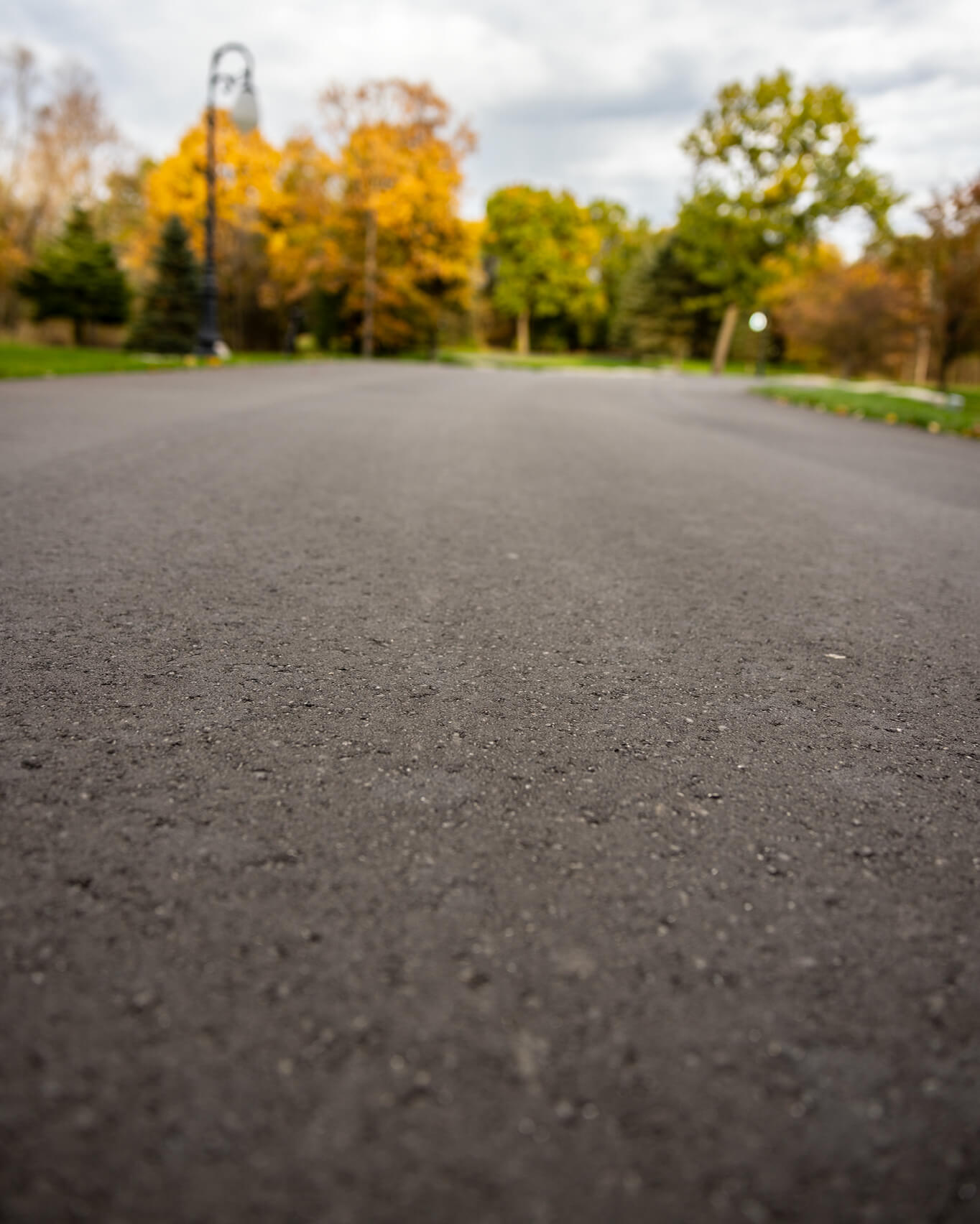
Asphalt driveways, asphalt roads, asphalt mixtures, asphalt parking lots and preventative maintenance. (Our CEO’s background is in education, and she says seven mentions of asphalt in one paragraph is the right number.)
Read on to learn how our favorite subject supports businesses, cities and homeowners in Detroit, Ann Arbor and beyond.
Even the very best pavement is similar. You can’t set it and forget. Yearly maintenance can give you 20–25 years, but a total repave is inevitable – especially in southeastern Michigan, where weather patterns are less predictable than the stock market.
So how do you know it’s time? The same way you check to see which of your teammates has too much on their plate or needs a vacation: look for signs of stress.
Frigid Januaries and boiling Julys, chemical spills and fatigue cracks are only a few factors that cause structural problems in your road, parking lot or driveway. Pooling water, large fissures and potholes are telltale signs of deeper problems. If these problems comprise more than 35% of your property, it’s time for a complete removal, regrade and replacement of your pavement.
Wondering whether it’s time for a full replacement? Email us or give us a ring at 734 · 929 · 0641 and we’ll provide a free inspection followed by honest advice. If another seal coat is all you need this year, that’s all we’ll recommend.
First, we grind away the top two inches of asphalt. Our tool for the job is a cold-plane milling machine. Its diamond-tipped teeth make quick work of the pavement’s top layer but leave the sub-base intact.
Second, we remove the ground-up asphalt from the work site and recycle it at a local asphalt manufacturing plant.
We then spray the exposed areas with SS1H tack coat, which ensures a strong bond between the old and new material. We then apply a new top layer of asphalt.
Finally, we restore the pavement’s intended grade by compacting it with a vibratory roller. It’s a bit like when an athlete drops into a massage chair after a strenuous workout. Without those good vibes, they’ll be limping the next day.
Aside from being eco-friendly, asphalt milling is also more cost-effective than a full rip-out and replace method. Compared with patching or overlays, which can begin to fail within the first year, milling extends the lifespan of your pavement for at least eight years.
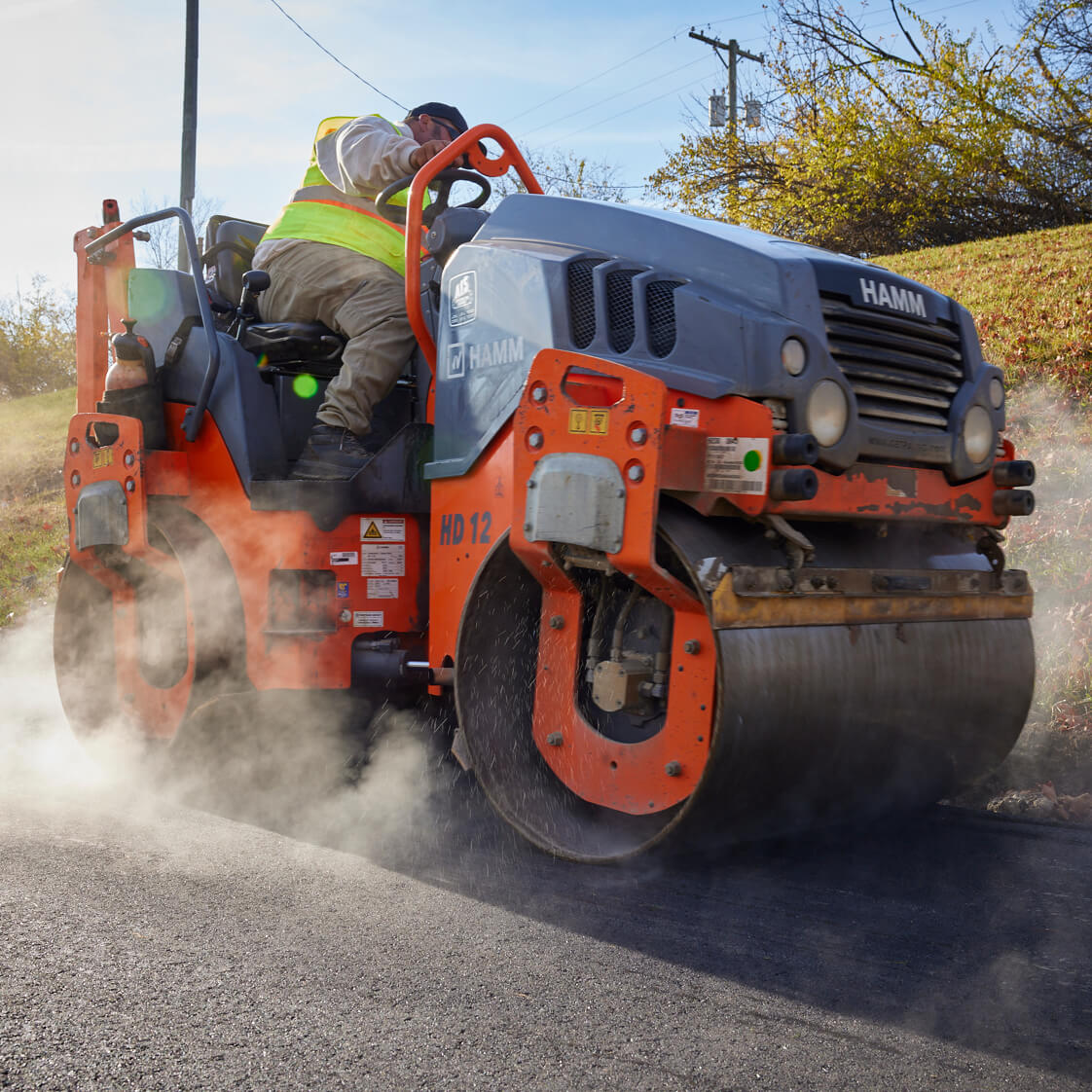
Long-lasting paving starts with thoughtful site planning that responds to the environment. The flow of water is everything: where it comes from, how it’ll drain and how we can minimize the impacts of rain, ice and snow.
You’ve heard it’s smart to measure twice and cut once. Our mantra – buy nice or buy twice – is never more true than with brand-new asphalt installation. That’s why carefully checking the property’s sub-base and grading the aggregate base are business as usual for us. You’ll get proper compaction and pavement that has a fighting chance against traffic and the elements.
You can set a reminder to thank us 20 years later.

With a single layer, you’ll spend less upfront but more over time. Eventually, little depressions or “bird baths” appear. Summer puddles become winter ice patches, accelerating the breakdown of your driveway. Plus, you probably don’t want to ice skate from your garage to the mailbox just to avoid wiping out on an icy spot. Unless you’re Scott Hamilton. Or Tom Cruise.
If you’d prefer a warmer analogy, let’s say it’s high summer. You’re boating on the lake or lounging on a tropical beach. If you only apply one layer of sunscreen in the morning, you’ll pay for it later. Apply twice, and you won’t feel like an overcooked lobster.
So don’t get burned. Rely on Sommerset to pave your driveway the right way.
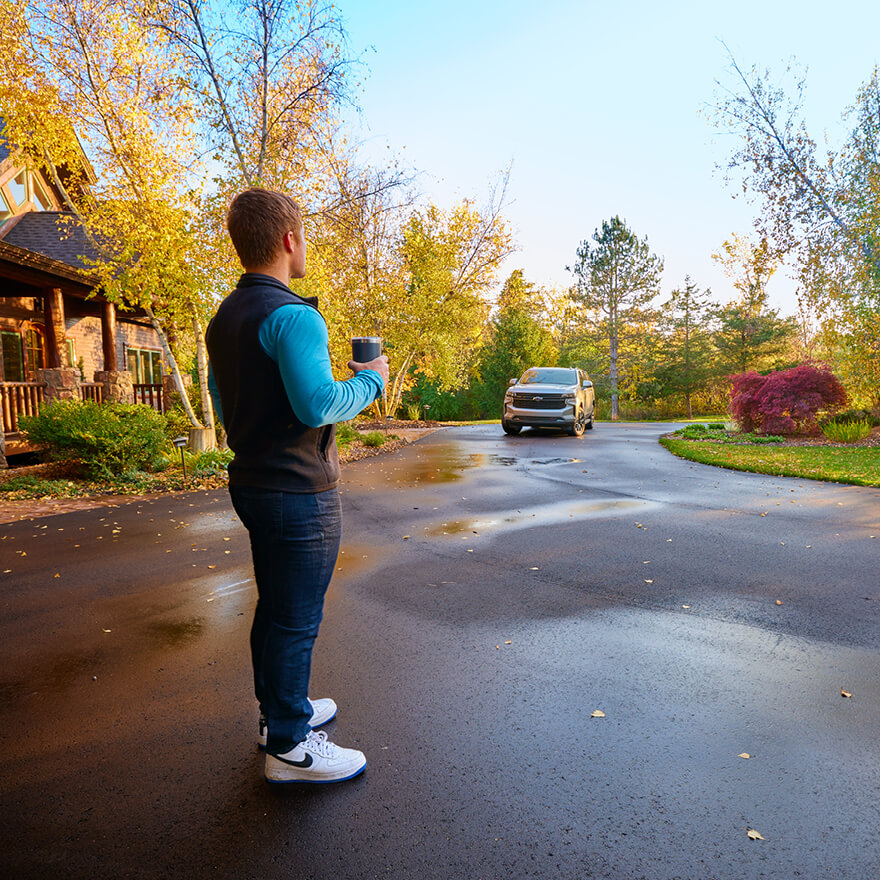
Municipal paving requires a list of bona fides and a price that maximizes a taxpayer’s dollar. Commercial jobs require building under traffic most of the time and are time-sensitive 101% of the time. And nothing’s more personal than your own driveway – the final stop on your way home.
Get a free quote today, or dig into the links below to learn more about how we approach projects like yours.
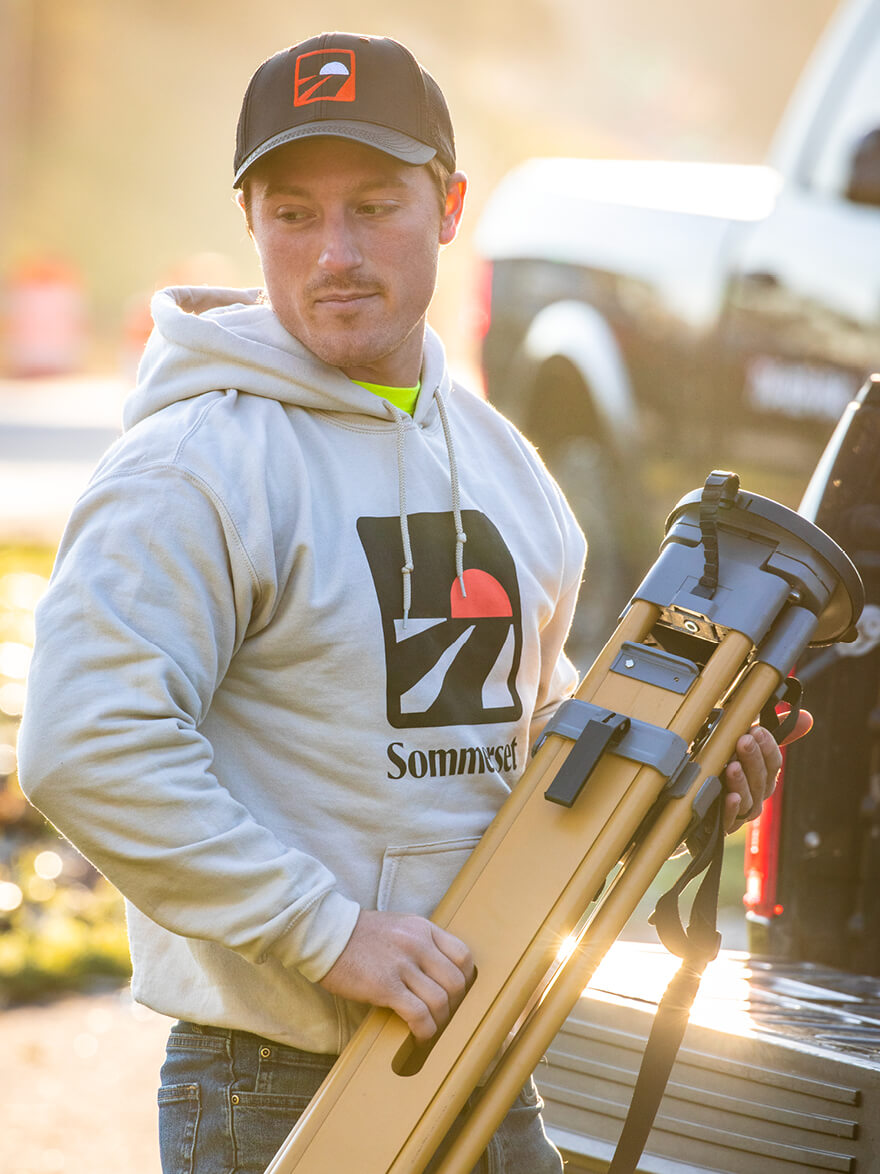
Other Services We Offer
We couldn’t call ourselves a legit paving company if we weren’t well-acquainted with the full range of paving materials and processes.
For instance, our commercial and municipal projects often involve concrete work in addition to asphalt. Or if you’re a homeowner who prefers concrete for your driveway, we’ve got you covered.
No matter the substrate and no matter the project size, we apply the same exacting standards every time. Check out the pages below to learn more about our range of services.
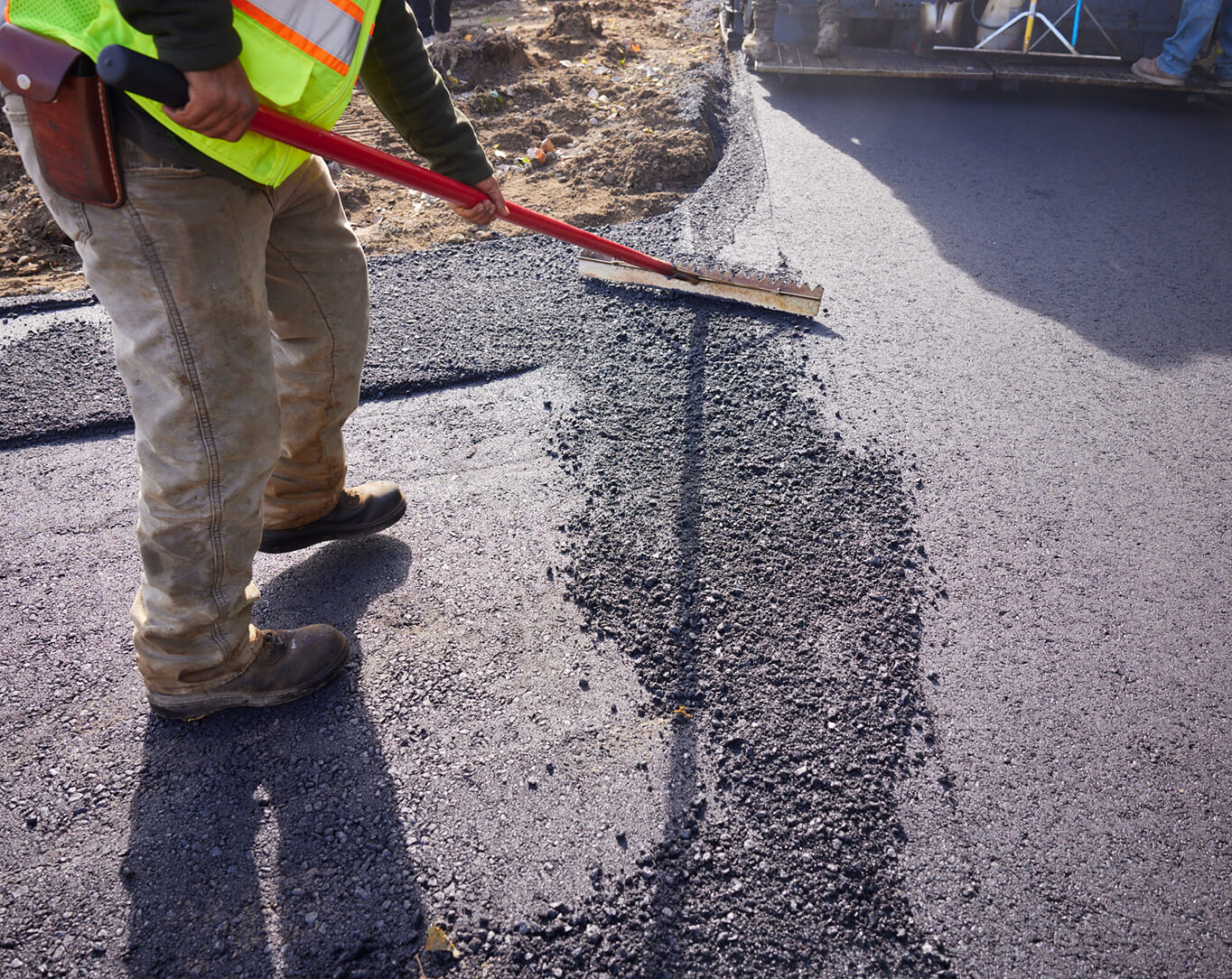
In 2021, a contractor finished building a vast car distribution center in Michigan. It only took two years for the parking lot to fall apart.
The job was never going to be easy. The terrain is flat and swampy, and the water table is so close to the surface that the contractor couldn’t build catch basins to help keep the parking lot dry.
It was a tall order, for sure. But not impossible.
The contractor’s first mistake was choosing expedience over good compaction. They extended the paving machine’s arms to maximum length, hoping to shave hours and dollars by spreading the asphalt as quickly as possible. The machine’s screed didn’t vibrate as intended, leading to uneven asphalt with poor density and low spots just waiting to hold water.
Sure enough, rainwater soon soaked through the spongy asphalt and pooled in the many indentations. In a matter of months, massive cracks opened up.
The situation would’ve been a safety hazard and an eyesore in any parking lot. But for a property meant to accommodate hundreds of vehicles every day, it was a catastrophe.
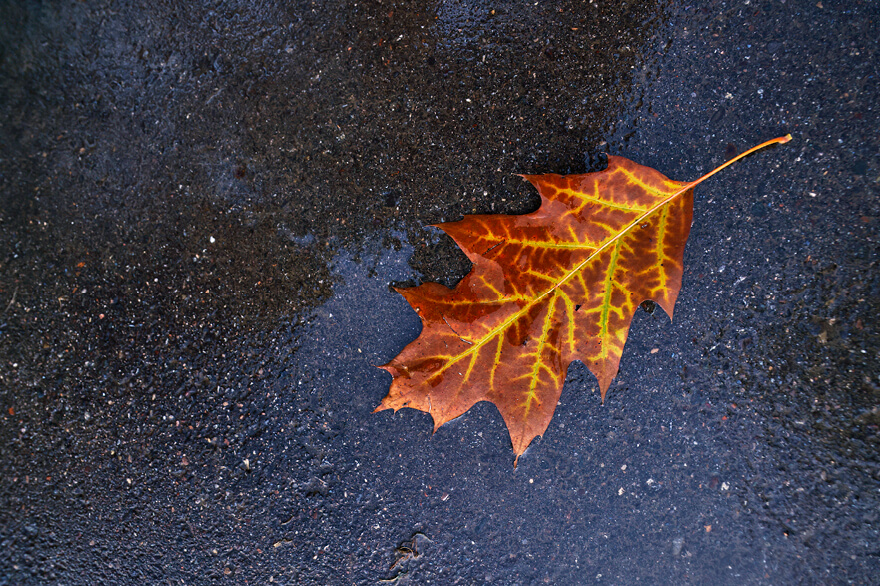
The client’s first mistake? Choosing a paving company based on price and ending up with a soggy money pit.
After a series of band-aid solutions, they realized it was past time for more comprehensive repairs and called Sommerset Paving.
If the client could rewind the clock and asphalt the Sommerset way, how would we do things differently?
To start, we’d apply our civil engineering knowledge and propose a plan for water drainage. Each of our pavers would have heated, vibratory screeds to ensure proper compaction. We’d use heat guns to test the asphalt for optimal temperature before compaction – a step we take in every project.
Sure, hindsight is 20/20. But the fact is, the process you just read about is business as usual at Sommerset.
If you want beautiful, long-lasting asphalt paving that’s tailor-made for southeastern Michigan’s weather and terrain, let’s talk.
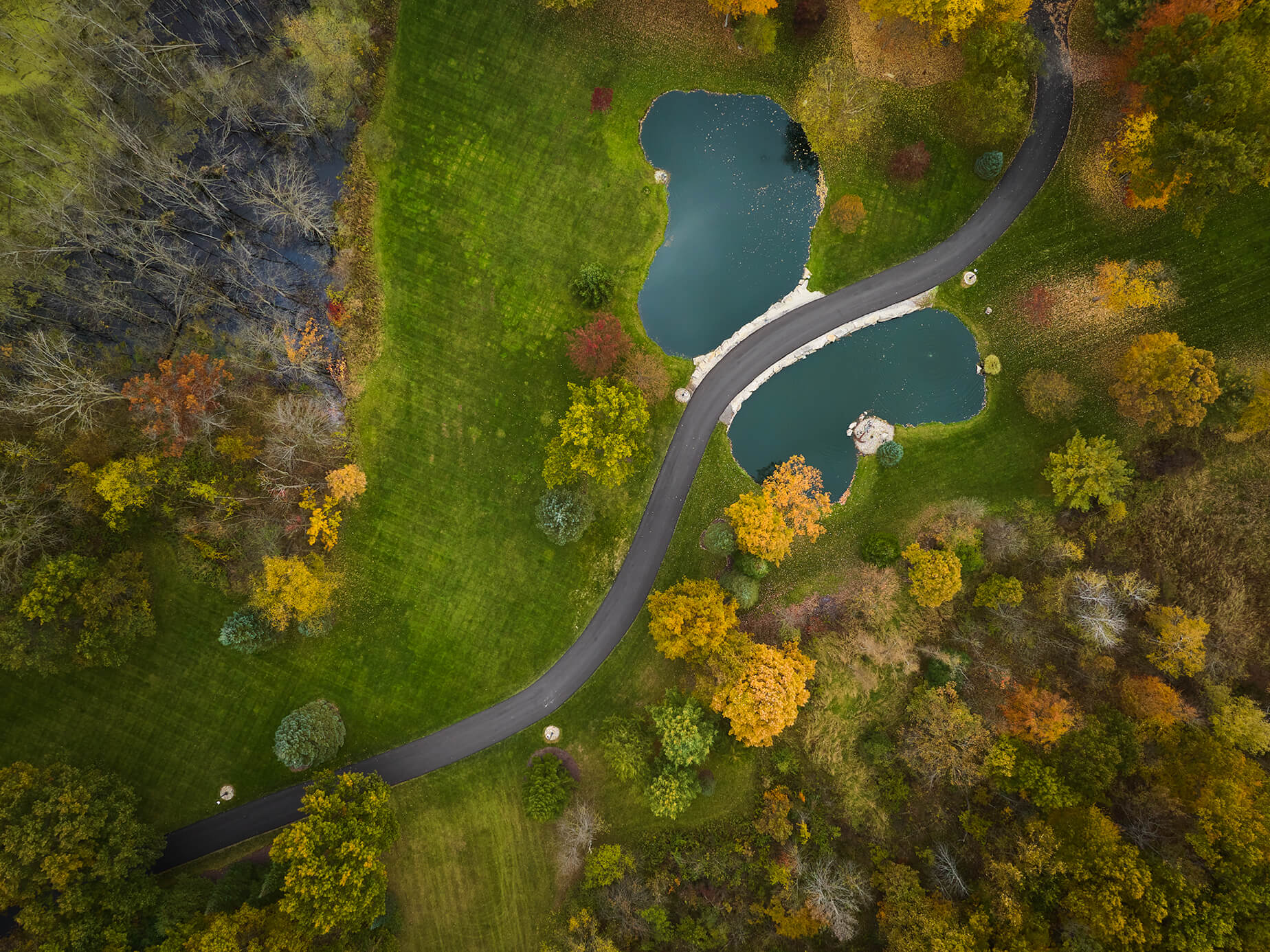